HPL laminate Compact with white core
Compact high pressure laminate in standard quality according to EN 438-9:BCS. With uniform white-coloured core and decorative melamine resin surface on both sides.
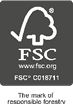
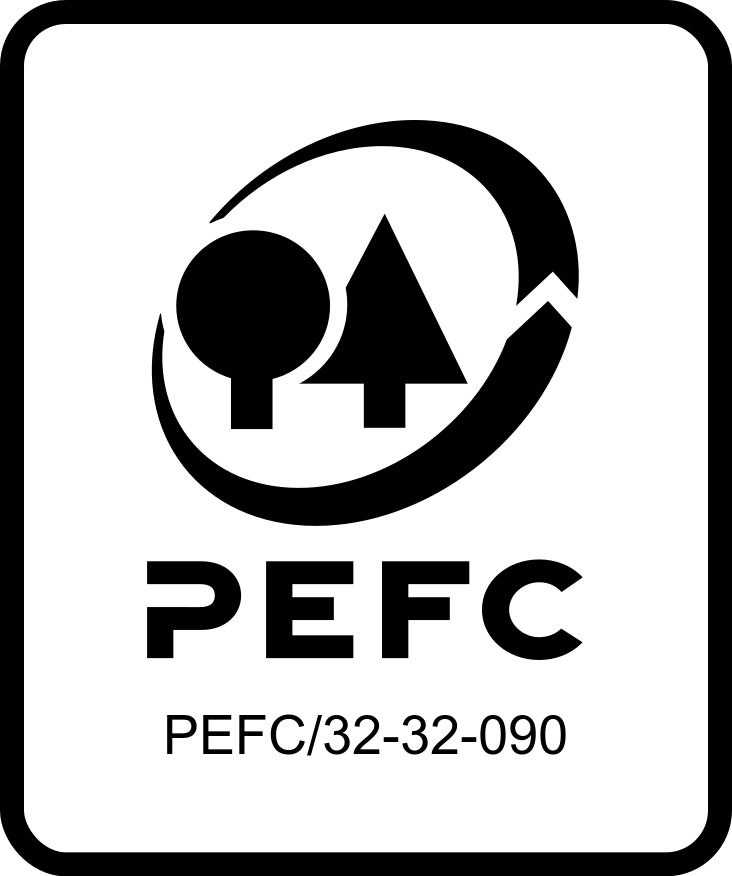

Areas of application
-
Furniture construction & interior fitting
Product features
-
Impact resistance
-
Low formaldehyde emission
-
Materials with higher damp resistance
-
Anti-fingerprint
-
Antibacterial
-
Easy care
-
Improved scratch resistance
-
Suitable for contact with food
FORMATS
Długość (mm) | Szerokość (mm) | Łączna grubość (mm) | Struktury |
---|---|---|---|
2.800 | 2.070 | 2 | 3 | 4 | 5 | 6 | 7 | 8 | 9 | 10 | 12 | 13 | 15 | HG | MO | MP | SM | VV |
4.100 | 1.300 | 4 | 5 | 6 | 8 | 10 | 12 | CM | GR | MP | RC | TC | VE | VV |
Brochures & Certificates
-
Blue Angel - Ecolabel certificate (RAL DE-UZ 76) – decorative compact high pressure laminate
PDF (150 KB) -
Declaration of the origin of wood (EUTR) - 1
PDF (382 KB) -
Declaration of the origin of Wood (EUTR) - 2
PDF (39 KB) -
Duropal Sustainability statement – Blue Angel DE-UZ 76 (High Pressure Laminate / Compact High Pressure Laminate / Flat bonded element)
PDF (377 KB) -
FSC _Certificate _Woodeco_valid by 16.10.2026
PDF (2 MB) -
REACH declaration_EN
PDF (500 KB)
decors
Product processing
- Please note that due to their material composition, through-dyed laminates are somewhat harder and more brittle than classic laminates with dark phenol resin core and are subject to marked warp in the event of climate fluctuations.
- Sufficient conditioning is required prior to installation and assembly. The premises themselves need to be at the normal climatic conditions in which the material will later be used.
- For an optimum result when cutting to size we recommend the following measures:
- Use a universal saw blade with chamfer (WZ/FA), e.g. GlossCut sawblade made by Leitz
- Hollow ground or trapezoidal tooth sawblades with negative tooth angle
- Optimized height adjustment of the sawblade
- Use universal scoring unit
- Use e.g. a pressure bar or pressure strip to prevent vibration of the material
- Work with lower feed rate than for standard laminates - Use a flat, firm surface to saw and drill on.
- Please note that sharp curring and quiet running tools are indispensable for perfect results.
- Drillholes must be countersunk. Through holes must be made oversize.
- Cutouts and inside corners must have a minimum radius of 8 mm to prevent notch stresses and therefore possible subsequent formation of cracks.
- To avoid chatter marks, cutting tools with high true-running are required. The feed rate is to be reduced in edge-corner and interface areas.
- Cut edges and surfaces should be finely re-sanded to improve surface roughness and ease of cleaning and possibly treated with polishing paste.
- It is possible to refinish narrow surfaces:
1. Dry grinding with 120/ 220/ 400 grit
2. Wet grinding with 600/ 1000/ 1500/ 2000 grit
3. Polish with nonwoven disc (6000 grit) and polishing paste - Please respect the recommendations of BLFA (www.blfa.co.uk) an ICDLI (www.icdli.com) for the processing of high pressure laminates.
- We recommend carrying out your own tests depending on the respective application and material requirement.
- Can be worked with carbide (HW) or diamond (DP) tipped tools on conventional woodworking machines.
- Keyhole saws, punches and jars are not suitable.
- Can be worked with carbide (HW) or diamond (DP) tipped tools on conventional woodworking machines.
- Keyhole saws, punches and jars are not suitable.
- All conventional removable and non-removable fittings for solid wood and wood materials are suitable.
- Sufficient conditioning is required prior to installation. The premises themselves need to be air-conditioned according to the future use.
- Where panels are covered with protective films, these must be removed from both sides of the panel at the same time to avoid warping. Remove the protective film before using the product, six months after delivery at the latest.
- The material is not suitable for areas subject to large fluctuations in temperature and humidity.
- Ensure good rear ventilation and climate equilibrium on both sides in the installed condition. For adequate air circulation the void should be at least 20 mm. It is important to interrupt horizontal substructures as well as the top and bottom ends of the wall panelling so that vertical rear ventilation is possible. Avoid direct fixing on the surface without air gap.
- Make sure that expansion of installed elements is not prevented. Please observe that when panels are combined with other materials their coefficients of expansion may differ.
- Ensure adequate room for movement of the panel material in the installed condition. Panel joints are to be made with oversize joints and throughholes.
- Newly built walls (made of brick or concrete or plastered walls) contain considerable amounts of moisture. Before covering them with panels they must be completely dried out.
- The base may not be moist or instable. Please make sure that minimum carrying capacity and stability correspond to the usage.
- Protect the substructure against corrosion.
- Avoid direct exposure to heat and any possible dehydration of the surfaces by light- or heat radiation or by air currents from heating- or air conditioning systems.
- Especially for large applications, we recommend paying attention to the colour and texture unifomity of the boards and cut products used when further processing and installing and that the production direction is taken into account.
- Please ensure that the material is processed and fitted correctly and using the best available technology.
- For further information on processing and installation of HPL and compact HPL, please respect the recommendations of ICDLI (www.icdli.com).
- Please note that due to their material composition, through-dyed laminates are somewhat harder and more brittle than classic laminates with dark phenol resin core and are subject to marked warp in the event of climate fluctuations.
- The material must be stored flat, level and horizontal on clean surfaces at normal climatic conditions (Temperature 18–25 °C, relative humidity 50–65 %).
- Avoid storage in the direct vicinity of thoroughfare gates, e.g. in the area of loading and unloading zones.
- Protect from moisture and wet conditions.
- Avoid direct exposure to heat and any possible dehydration of the surfaces by light- or heat radiation or by air currents from heating- or air conditioning systems.
- Avoid exposure to direct sunshine or UV rays, especially of products covered in film.
- Panels must be fully and horizontally stored with edges flush on a flat and clean base covered with plastic foil. Cover the top panel fully with foil and a cover board.
- These storage conditions must continue to be ensured after removing panels from the stack.
- Vertical storage is not recommended.
- Please note that incorrect storage, regardless of its duration, may cause irreversible distortion to the sheets.
- Foreign bodies or impurities in the pallet of sheets can lead to impressions and damage to the surface of the board.
- Sheets / boards must not be moved against each other ; they should be moved individually by hand or with suction equipment.
- Ensure that sufficiently large and sturdy bases, e.g. pallets, are used for the transportation of stacked sheets. The sheets on the pallet must be secured against slipping.
- Please wear the appropriate personal protective equipment (PPE) when processing and handling.
- The surface can be cleaned with water and gentle cleaning agents. To remove stubborn stains, please observe the recommendations in the data sheet "Cleaning of HPL surfaces" (www.icdli.com).
- We recommend energy recovery.
Processing
Machines and tools
Edging
Fitting technology
Installation and assembly
Storage, handling and transport
Health and safety
Cleaning and care
Disposal
Watch video